L’industria verde può trainare la riconversione di filiere legate a tecnologie ad alte emissioni, destinate ad uscire presto dal mercato. Per l’evoluzione della normativa, oppure per semplice ed ineluttabile mancanza di clienti.
Bisogna parlare subito di questo tema, guardando all’esempio di chi di treni ne ha persi pochi negli ultimi decenni. Come la Bosch, leader della componentistica automobilistica e gigante industriale con produzione che spazia dagli elettrodomestici alla robotica industriale.
Efficienza energetica
L’efficienza energetica è l’elemento chiave in quanto consente a macchinari e attrezzature di consumare meno energia.
È qui che entra in gioco la digitalizzazione, che permette anche di individuare con precisione in quale punto viene propria Energy Platform unita al software Nexeed per l’Inutilizzata l’energia.
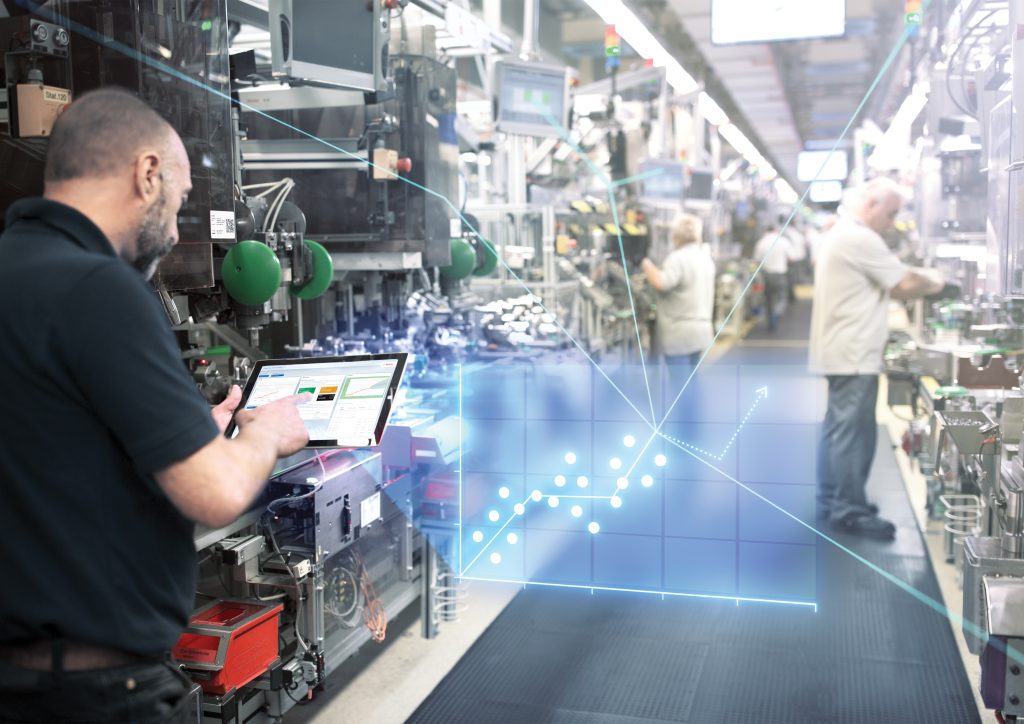
Per gestire il consumo di calore, elettricità e aria compressa, Bosch si affida alla propria Energy Platform unita al software Nexeed per l’Industry 4.0. In questo modo è più facile prevedere i consumi di energia, evitare i carichi di picco e riconoscere e correggere le deviazioni dei singoli macchinari.
Al momento la piattaforma viene utilizzata in più di 120 sedi aziendali e in oltre 80 progetti dei clienti.
Nello stabilimento Industry 4.0 di punta di Bosch, a Homburg, in Germania, questo software contribuisce a ridurre il fabbisogno energetico di oltre il 40% per ogni prodotto fabbricato.
Intelligenza artificiale
L’intelligenza artificiale offre ancora più possibilità. Nello stabilimento di Eisenach, sempre in Germania, Bosch sta conducendo un progetto pilota con la propria Balancing Energy Network. Basata sulla piattaforma di energia, questa soluzione di IA gestisce e ottimizza la richiesta di energia di 1.000 macchinari.
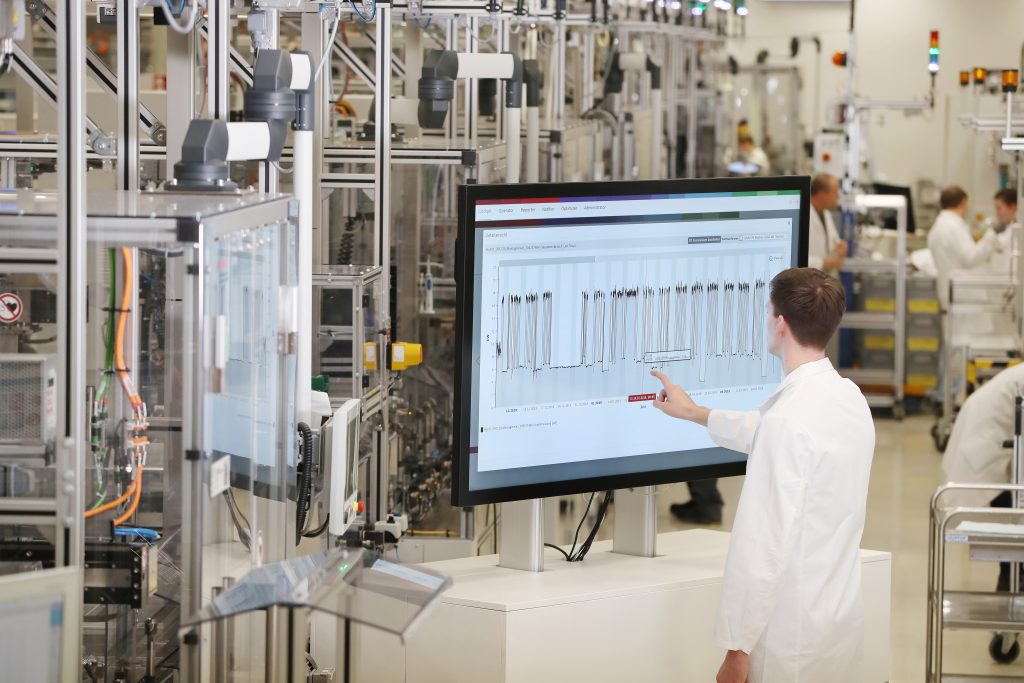
L’IA mostra la correlazione tra i dati di produzione e logistica, informazioni meteo e prezzi dell’energia e offre suggerimenti da mettere in atto. Secondo le proiezioni, l’IA consentirà di ridurre i costi di energia annui della sede di un ulteriore 5% circa.
Connessione e gemelli digitali
La connessione intelligente di macchinari e processi e la loro interazione con la tecnologia informatica e di comunicazione creano le basi per una produzione efficiente sotto il profilo energetico.
Sempre più funzioni saranno trasferite dall’hardware al software, anche grazie ai gemelli digitali.
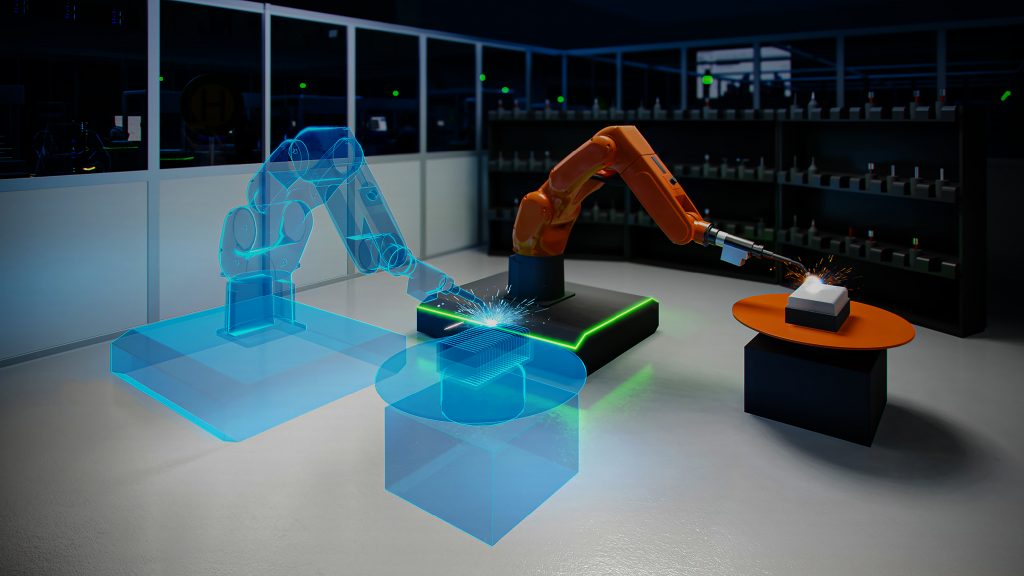
Secondo Rolf Nojork, responsabile Industrial Technology della Bosch:
Nella fabbrica del futuro sarà possibile regolare molti elementi semplicemente premendo un pulsante.
Bosch ha adottato dunque un approccio modulare. Gli unici elementi statici di una fabbrica così concepita sono il pavimento, il soffitto e le pareti.
Tutto il resto sarà dinamico e variabile, le macchine saranno costantemente disposte in nuovi assetti e cambieranno configurazione in base al lavoro da svolgere. Stabilimento e apparecchiature dureranno più a lungo e diminuirà la quantità di materie prime utilizzate per la produzione di nuovo hardware.
I gemelli digitali forniscono la capacità di progettare, sviluppare e testare i sistemi produttivi per renderli più efficienti in termini di consumo di risorse.
Le copie virtuali dei beni fisici nella fabbrica reale ci permettono di simulare e ottimizzare i flussi di lavoro e i processi, senza interrompere le attività
ha dichiarato Najork.